Discover critical insights into shot sleeves for aluminium die casting, including material science, performance data, and best practices to optimize durability and casting quality.
1. The Critical Role of Shot Sleeves in High-Pressure Aluminium Die Casting
Shot sleeves are the backbone of high-pressure die casting (HPDC) systems, acting as the conduit between molten aluminium and the die cavity. Their primary functions include:
- Controlled Metal Transfer: Directing molten aluminium into the die under pressures exceeding 1,000 bar.
- Thermal Management: Minimizing premature solidification by maintaining optimal metal temperature.
- Wear Protection: Shielding the die from direct exposure to high-velocity molten metal.
Key Performance Metrics:
- Cycle Consistency: A study by NADCA (North American Die Casting Association) revealed that shot sleeve wear contributes to 15–20% of casting defects like porosity and cold shuts.
- Lifespan: Premium shot sleeves endure 80,000–150,000 cycles under optimal conditions, while low-quality alternatives fail at 30,000–50,000 cycles.
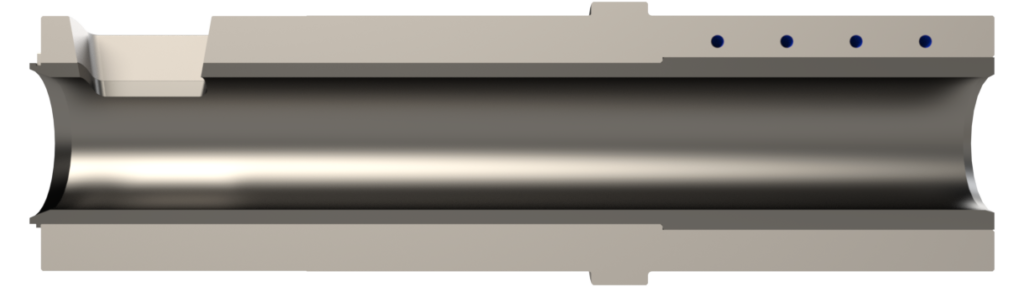
2. Material Selection: Balancing Durability and Cost
2.1 Industry-Standard Materials
Material | Hardness (HRC) | Thermal Conductivity (W/m·K) | Relative Cost |
---|---|---|---|
H13 Tool Steel H13 | 48–52 | 24–28 | $$$ |
H11 Tool Steel H11 | 46–50 | 26–30 | $$ |
Copper Alloy (CuCrZr) | 32–36 | 320–350 | $$$$ |
Data Insights:
- H13 Steel: The most widely used material, offering a balance of hardness (48–52 HRC) and thermal fatigue resistance. NADCA recommends H13 for >90% of aluminium die casting applications.
- Copper Alloys: Superior thermal conductivity (350 W/m·K vs. 28 W/m·K for H13) reduces thermal stress but increases costs by 40–60%. Ideal for high-volume production (e.g., automotive parts).
2.2 Advanced Coatings for Enhanced Performance
- Plasma Nitriding: Increases surface hardness to 1,200–1,500 HV (vs. 500–600 HV for uncoated H13), extending lifespan by 30–50%.
- Tungsten Carbide (WC) Overlays: Reduce abrasive wear by 70% in high-silicon aluminium alloys (e.g., A380, A383).
3. Precision Manufacturing & Heat Treatment Protocols
3.1 Dimensional Tolerances
Parameter | Tolerance | Impact on Casting Quality |
---|---|---|
Inner Diameter | ±0.02 mm ±0.02 | Ensures consistent fill rates |
Straightness | ≤0.05 mm/m | Prevents turbulence-induced porosity |
Surface Roughness | Ra ≤0.8 μm | Reduces piston friction |
3.2 Heat Treatment Process
- Vacuum Hardening: Heated to 1,020–1,050°C, followed by oil quenching to achieve core hardness of 48–52 HRC.
- Tempering: Double tempered at 550–600°C to relieve internal stresses.
- Induction Hardening: Localized hardening of the inner bore to 55–60 HRC (depth: 2–3 mm).
Case Study: A European automotive supplier achieved a 22% reduction in sleeve replacement frequency after switching to induction-hardened H13 sleeves.
4. Lubrication Strategies to Mitigate Wear
4.1 Graphite vs. Water-Based Lubricants
Lubricant Type | Friction Coefficient | Thermal Stability | Residue Formation |
---|---|---|---|
Graphite | 0.08–0.12 | Up to 1,200°C | Moderate |
Water-Based | 0.15–0.20 | Up to 800°C | Low |
Recommendation: Graphite lubricants are preferred for aluminium die casting due to superior high-temperature performance.
4.2 Lubrication Automation
Automated spray systems (e.g., LubriLine 5000) reduce lubricant consumption by 35% while ensuring uniform coverage.
5. Extending Shot Sleeve Lifespan: Data-Driven Best Practices
5.1 Maintenance Protocols
- Daily: Inspect for scoring or cracks using boroscopes.
。 - Weekly: Measure inner diameter wear with laser profilometers (max allowable wear: 0.1 mm).
- Monthly: Recoat sleeves showing >10% hardness loss.
5.2 Operational Adjustments
- Slow Shot Phase: Optimize plunger speed to 0.2–0.5 m/s to minimize turbulence.
- Metal Temperature: Maintain aluminium at 660–680°C (eutectic point) to reduce thermal shock.
Case Study: A Chinese manufacturer reduced shot sleeve replacement costs by $18,000/year by implementing real-time temperature monitoring.
6. How to Select the Right Shot Sleeve: A Decision Matrix
Application | Recommended Material | Coating | Expected Lifespan |
---|---|---|---|
High-Volume Auto | CuCrZr + WC Overlay | Plasma Nitrided | 120,000–150,000 cycles |
Low-Volume Electronics | H13 Steel H13 | Uncoated | 60,000–80,000 cycles |
Expert Tip: Partner with suppliers offering 3D laser scanning for sleeve inspection (e.g., SleeveCheck Pro).
7. Industry Trends & Innovations
- Additive Manufacturing: Laser-cladded sleeves with gradient materials (steel core + nickel alloy surface) show 40% higher thermal fatigue resistance.
- IoT Integration: Sensors monitoring sleeve temperature and wear in real-time (e.g., SmartSleeve™) reduce unplanned downtime by 25%.
Conclusion 结论
Selecting and maintaining shot sleeves for aluminium die casting requires a scientific approach combining material science, precision engineering, and data-driven maintenance. By adopting advanced materials like induction-hardened H13 or CuCrZr alloys, implementing automated lubrication, and leveraging IoT-enabled wear monitoring, manufacturers can achieve:
- 20–30% longer sleeve lifespan
- 15% reduction in casting scrap rates
- Annual cost savings exceeding $50,000 for high-volume operations
For further technical specifications, download our Shot Sleeve Selection Guide or consult our engineers via
Internal Links: 内部链接: