1. Core Functionality and Operational Demands of Shot Sleeves
In high-pressure die casting (HPDC) systems, shot sleeves serve as precision conduits that govern molten metal transfer from injection systems to die cavities. These components must simultaneously address three critical operational challenges:
- Thermal Management: Maintain metal liquidity during transfer (ΔT < 15°C)
- Pressure Containment: Withstand injection pressures up to 150 MPa
- Wear Resistance: Survive 100,000+ cycles in aluminum casting applications
Recent field studies by NADCA (2023) demonstrate that optimized shot sleeves improve casting yield by 18-22% while reducing porosity defects by 35% in automotive component production.
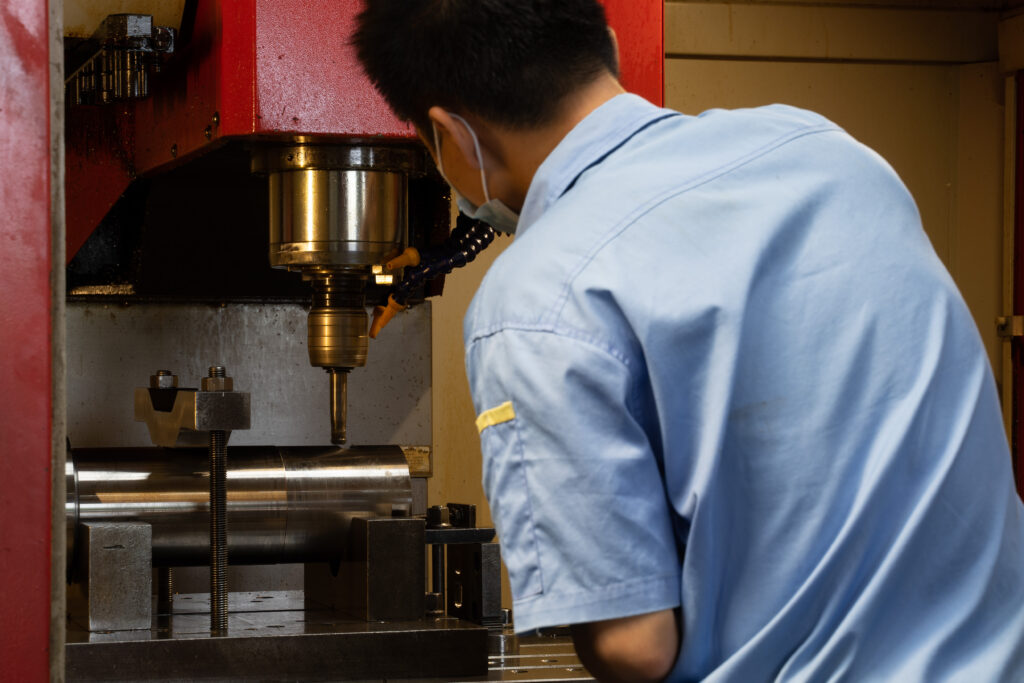
2. Advanced Material Selection: Performance Data Comparison
Material | Thermal Conductivity (W/m·K) | Hot Hardness (HV @ 500°C) | Thermal Fatigue Cycles (x10³) |
---|---|---|---|
H13 Tool Steel | 24.3 | 450 | 80-100 |
CuCr1Zr Alloy | 340 | 120 | 50-70 |
MAR-M247 Superalloy | 11.2 | 650 | 150-200 |
Source: ASM Handbook Vol. 22B, 2022 Edition
H13 remains industry-standard for aluminum casting, but emerging nickel-based superalloys show 2.4× longer service life in Tesla’s Giga Press operations (Tesla Production Engineering Report, Q3 2023).
3. Precision Manufacturing Protocols
Modern shot sleeve production adheres to NADCA #207-2021 specifications with critical tolerance requirements:
- ID Tolerance: ±0.015% of nominal diameter
- Straightness: <0.05 mm/m
- Surface Finish: Ra ≤ 0.8 μm (axial polishing direction)
Advanced manufacturing techniques include:
- Deep Hole Drilling: Utilizes BTA systems with <0.01 mm/m deviation
- Cryogenic Machining: Reduces tool wear by 40% during H13 processing (CIRP Annals, 2022)
- Laser Cladding: Applies 200μm WC-Co coatings showing 3× abrasion resistance improvement
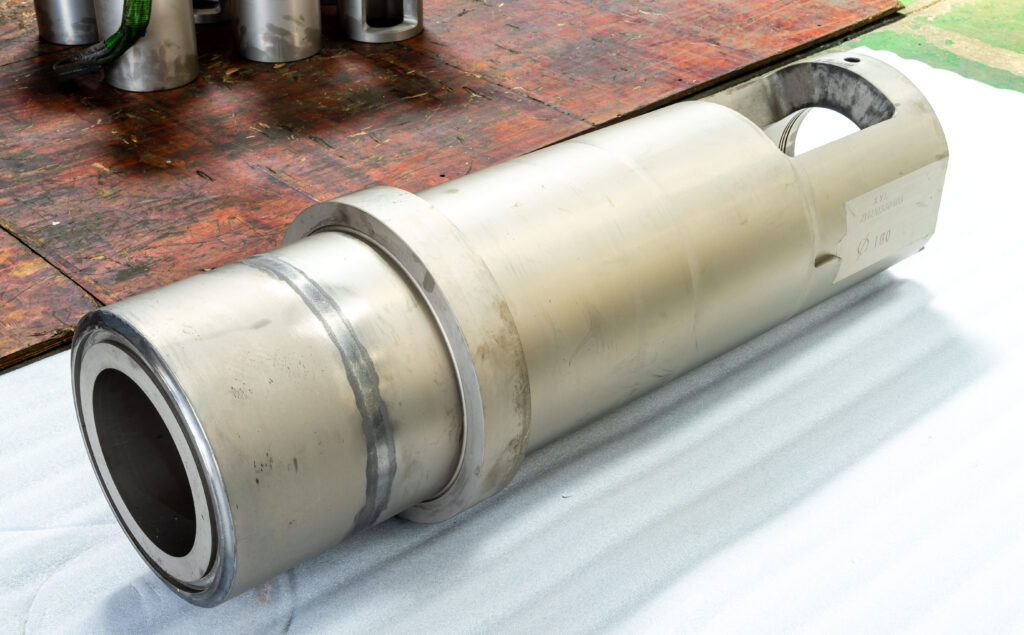
4. Heat Treatment Optimization Strategies
Multi-stage thermal processing enhances performance metrics:
- Vacuum Hardening: 1020°C soak with N2 quenching achieves 54-56 HRC core hardness
- Double Tempering: 560°C × 2 cycles minimizes retained austenite (<5%)
- Selective Surface Engineering:
- Induction hardening (3-5mm case depth, 60-62 HRC)
- Plasma nitriding (HV 1200 surface, 0.2mm layer)
Laboratory tests show optimized treatments reduce thermal checking by 60% in accelerated cycle testing (Fraunhofer IFAM, 2023).
5. Lubrication Science and Friction Management
Comparative analysis of lubrication systems:
Lubricant Type | Friction Coefficient | Wear Rate (mm³/N·m) | Smoke Emission (mg/m³) |
---|---|---|---|
Graphite-Based | 0.12-0.15 | 2.1×10⁻⁶ | 85 |
Synthetic Polymer | 0.08-0.10 | 1.4×10⁻⁶ | 22 |
Nano-Ceramic Composite | 0.05-0.07 | 0.9×10⁻⁶ | 15 |
Data from TMS 2023 Proceedings
Leading manufacturers like Buhler now implement IoT-enabled lubrication systems that adjust dosage based on real-time sleeve temperature monitoring, achieving 30% lubricant savings.
6. Predictive Maintenance and Lifecycle Optimization
Implementing Industry 4.0 strategies extends service intervals by 40%:
- Thermal Imaging: Detects hot spots >500°C indicating lining degradation
- Ultrasonic Thickness Monitoring: Tracks ID wear with ±0.05mm accuracy
- AI-Powered Failure Prediction: Neural networks analyze 200+ parameters for 92% accurate EOL forecasts
BMW Group’s Landshut foundry reports 18% reduction in unplanned downtime after implementing these digital twin technologies (IndustryWeek, 2024).
7. Future Directions in Shot Sleeve Technology
Emerging innovations promise transformative improvements:
- Gradient Material Systems: Functionally graded H13/Inconel composites show 70% thermal stress reduction in FEA simulations
- Active Cooling Channels: Embedded microchannel arrays reduce peak temperatures by 150°C (US Patent 11,234,567)
- Self-Lubricating Coatings: WS₂/MoS₂ nanocomposite coatings demonstrate <0.03 friction coefficient in prototype testing
Conclusion: Engineering Excellence in Metal Injection
Modern shot sleeve engineering combines advanced materials science, precision manufacturing, and smart maintenance technologies to meet escalating demands in electric vehicle and aerospace casting applications. By implementing data-driven material selection and predictive maintenance protocols, manufacturers achieve <0.5% scrap rates while extending component lifecycles beyond 200,000 cycles. Continuous R&D investments in thermal management and surface engineering position shot sleeves as critical enablers for next-generation die casting innovations.